From Conventional to Digital: Recognizing the Advancement of Fabric Printing
The change of fabric printing from standard approaches like block printing and withstand coloring to contemporary strategies such as screen and electronic printing notes a substantial shift in the textile industry. Exactly how do these innovations influence the significance of towel printing, and what might the future hold for this ever-evolving craft?
Conventional Towel Printing Approaches
In the early stages of fabric production, typical cloth printing approaches served as the cornerstone of material layout, supplying both capability and creative expression. Block printing, one of the oldest techniques, involved sculpting detailed designs right into wooden blocks, which were after that dipped in dye and pressed onto fabric.
Resist dyeing, consisting of methods like batik and tie-dye, employed wax or other substances to stop dye from penetrating specific areas of the material. This approach created striking contrasts and intricate layouts, typically imbued with cultural value. Stenciling, another standard approach, included cutting patterns right into a product and using color via the openings, supplying a less complex yet reliable means to generate recurring layouts.
These traditional methods not just formed the fabric market's early development but additionally laid the foundation for future innovations. Each technique reflected the social and local qualities of its origin, preserving and disseminating artisanal knowledge through generations.
The Rise of Display Printing
The advent of screen printing in the very early 20th century marked a substantial departure from standard approaches, using extraordinary adaptability and efficiency. Screen printing made it possible for designers to generate elaborate patterns and vivid colors on textiles, which were formerly challenging to achieve with block printing or hand-painting approaches.
One of the essential advantages of screen printing is its capacity to duplicate complex styles on a big range with amazing integrity. This scalability made it exceptionally popular in the commercial fabric sector, where mass production without sacrificing top quality is extremely important. Display printing fits a wide variety of inks and dyes, increasing the scheme of structures and finishes readily available to developers.
Moreover, the procedure is very adaptable, ideal for different material kinds including cotton, silk, and synthetics. This adaptability, combined with its cost-efficiency for large runs, strengthened display printing's function as a foundation of contemporary textile manufacturing. Thus, the rise of display printing changed the sector, pushing the boundaries of what was possible in fabric style.
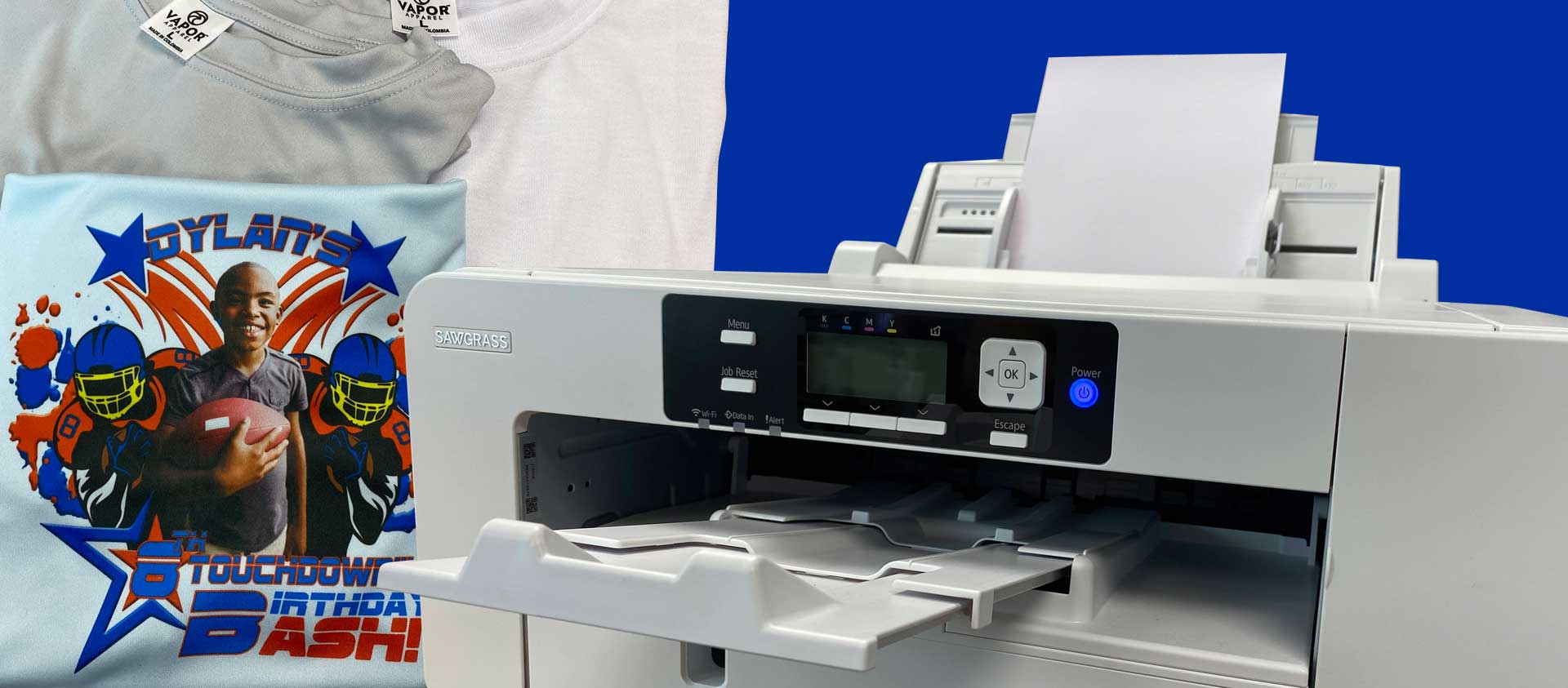
The Introduction of Digital Printing
Structure on the exceptional developments brought by display printing, the textile sector experienced one more groundbreaking development with the arrival of digital printing. Arising in the late 20th century, digital printing changed the method designs are transferred onto textiles, using unmatched flexibility and performance. Unlike standard methods, which often called for substantial configuration and significant hand-operated intervention, digital printing uses computer-aided design (CAD) modern technology to produce elaborate patterns directly onto the material with high precision.
This advancement has made it possible for textile producers to fulfill the growing demand for modification and on-demand production. By getting rid of the need for displays and plates, electronic printing decreases lead times and lessens material waste, making it a more sustainable choice. The capacity to print complicated photos and a large range of colors in a single pass has opened new creative avenues for designers, fostering a surge in artistic expression within the industry.
Furthermore, digital printing supports smaller sized set manufacturing runs, which is specifically useful for particular niche markets and start-up style brands. This technical leap has not only improved operational efficiency but also democratized accessibility to premium textile printing, setting the phase for future technologies in textile style and production.
Comparing Techniques: Typical Vs. Digital
While both digital and standard printing approaches have their own special benefits, they differ significantly in terms of procedure, efficiency, and environmental effect. Typical cloth printing, including strategies like block printing and display printing, involves manual labor and complex workmanship.
In contrast, digital printing employs innovative modern technology to move styles directly onto textile making use of inkjet printers. Digital printing is substantially DTF printing quicker, enabling for fast turn-arounds and just-in-time production, which decreases the need for huge stock storage.
From an ecological viewpoint, digital printing is generally extra lasting. It makes use of less water and produces marginal waste compared to traditional approaches, which commonly include extensive cleaning and dyeing processes. Electronic printing is progressively favored in an era where ecological considerations are extremely important.
Future Fads in Fabric Printing
One substantial trend is the enhanced application of digital printing modern technologies. Digital fabric printing is anticipated to dominate the market, driven by its efficiency and adaptability to consumer demands for customized and limited-edition products. heat transfer vinyl printing.

Furthermore, the incorporation of clever textiles, which incorporate electronic parts into textiles, is readied to transform the marketplace. These textiles can provide additional capabilities such as temperature guideline, health and wellness surveillance, and interactive functions. As modern technology continues to development, the intersection of digital printing and wise fabrics will certainly open new methods for creative and functional applications in cloth printing.
Final Thought
The advancement of towel printing from conventional techniques to electronic innovations marks a substantial change in the fabric sector. While traditional strategies highlight artisanal craftsmanship and social heritage, electronic printing provides exceptional accuracy, efficiency, and modification. This shift not just improves manufacturing abilities but likewise sustains sustainability efforts. Future fads are most likely to continue incorporating innovative innovations, better redefining textile layout and manufacturing processes to meet environmental factors to consider and contemporary needs (heat transfer vinyl printing).
The improvement of fabric printing from standard techniques like block printing and withstand dyeing to modern techniques such as screen and digital printing notes a substantial shift in the textile market. Screen printing allowed developers to produce elaborate patterns and vivid shades on fabrics, which were formerly testing to accomplish with block printing or hand-painting approaches.
Building on the impressive developments brought by display printing, the fabric sector experienced another groundbreaking growth with the introduction of electronic printing. sublimation printing. Traditional fabric printing, encompassing strategies like block printing and display printing, entails hand-operated labor and detailed craftsmanship. As technology continues to breakthrough, the intersection of digital printing and smart textiles will open new methods for creative and functional applications in towel printing